Quality and Attention to Detail – Why it is so important to us!
If you have been to a local market, souvenir store, or even ordered online, you can see that the maker community is filled with many different forms of art, and there are more people making similar items to what we do, and that’s ok! At first glance, you might think a lot of it looks alike, even mass-produced, so how do you know what to choose? At CestCreative, we have invested in top quality equipment, spent years learning and dialing in settings, honed our design skills, and we use this experience to deliver what we believe to be top quality products at fair prices. Not only do we make the items you see, we also sell some of the digital files to other makers (ask me sometime about those viral “Stanley Toppers” and how our $1.99 file paid off someone’s Mira 7 in 19 days!!!). We also support other designers and purchase files to use in our products, so it is possible that we could be selling something that looks the same as another seller – because they bought the same file too. How we adapt these designs may be limited to the terms and conditions of the seller, but we try to give the finished product our own flare so that in the end, you get a customized piece that reflects your vision, your colors, and your style. That’s who we are – CestCreative. Personal. Creative. You.
So what can you look for, and how can you tell we put our love and attention into every piece that we make?
- We ask a lot of questions up front to ensure that we are capturing your style and vision for your project.
- For printed items, we require high quality images
- We do not deal with copyright/trademarked items unless you have authorization (example: photographer release to print images, you are a representative of the company or organization providing the logo, etc)
- Finishes are clean, no jagged edges, sloppy paint, char, shadows, and that engraved logo shines as bright as the rim!
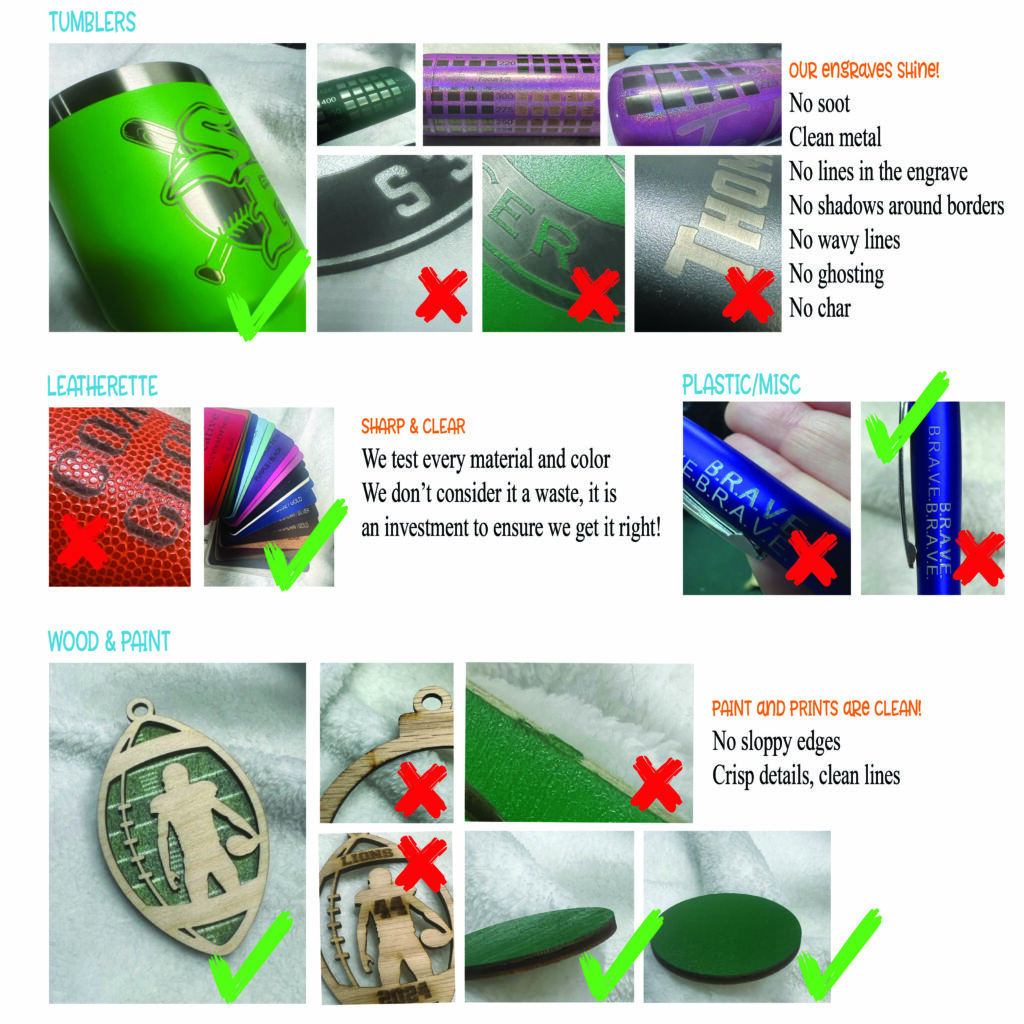
We know you have many choices and we THANK YOU for choosing us for your personalized gifts!
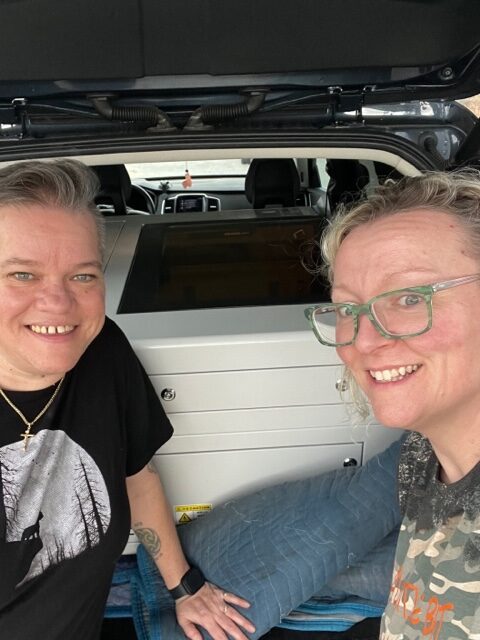
This is when we picked up our Mira 7!
As you all have seen on social media, I am trying to win an Aeon Laser USA Mira 7! One of ways that I can enter is to share different features that I love about my lasers! I can say a lot …so I am going to try to keep it simple! You too can win a laser at www.aeonlaser.us/contest from June 26 – July 14!
First post – I am here to tell you about the red dot pointer on the laser head. You can see my little video on TikTok, Insta, YouTube, and my personal FB page – but to give you an idea of why I love it so much, I need to describe the “old way”. You see, I started with a smaller hobby laser that didn’t have this feature. It has a camera which gets you close – but this red dot on the Aeon lasers really is precise and I can move it anywhere on the 24″x36″ (approx) Mira 9 bed! And for my Mira 7 – I have that set up for tumblers – I can get the logos EXACTLY where I want them! So instead of being “in the ballpark” or “close enough” I am literally “spot on”!
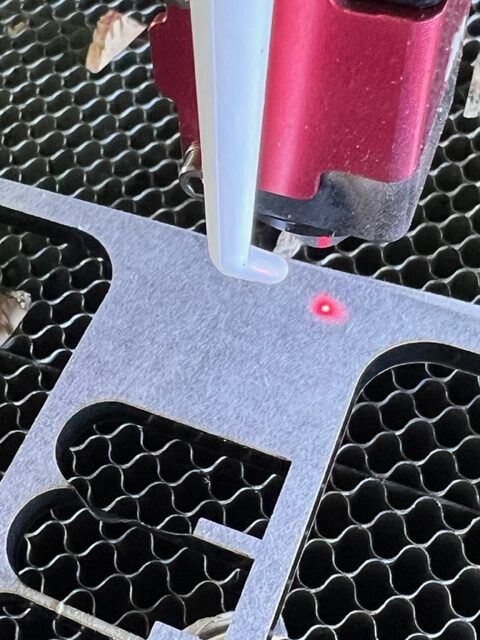
Another reason I love my Aeon Lasers… INNOVATION!
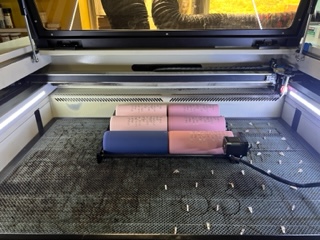
Ok, let’s talk about innovation. When you think about lasers, you might think about an 80s movie called REAL GENIUS where students worked on lasers and eventually shot them from the sky and popped a house full of popcorn… No? Am I showing my age? Well lasers are innovative in and of themselves. They are a super cool tool that really haven’t been around “that long” at least in the small business space. The fact that I can say that I have more than one IN MY BASEMENT! is a bit crazy to think about!
But if lasers are innovative – what makes AEON Lasers special?
Well, that’s a great question and one that I asked the president of AEON Laser USA when I visited the site in January 2023. There are several things that AEON Laser USA does to the machine after it comes from the overseas manufacturer and before it is delivered to the end-customer. Internal goodies that you may never have a need to see – but that just make the machine operate more efficiently, makes updates and repairs easier, or even – some enhancements that have even been backward integrated into the manufacturing process.
But what about innovations outside of the guts, nuts, and bolts? Did you know that AEON Laser USA invented this multi-roller that can be used to engrave 6 cups? One of the inefficiencies of tumbler engraving is swapping out the cup – taking it on and off the rotary. Well, now, you can set up your project ONCE, line up your cups ONCE, and eliminate 5 intermediate steps!
Size Matters
Let’s get the technical stuff out of the way – today I am telling you about my Mira 9 from Aeon Laser USA which has a bed size of 900mm wide x 600mm deep. We are just going to call that 24×36 inches ok? Cool.
So as you can imagine, going from a hobby laser with a bed size of 12×20 which is totally misleading because the cuttable area was more like 10.8×18…,to a commercial machine with more than double the space was a huge (literally!) win for us! I had grandiose ideas of all of the big signs that I would cut when she arrived, but to be honest, I mostly cut more smaller items – which is also great because I am not changing out sheets every 5 minutes.
The large bed size is perfect for large signs (I cut my own rounds now instead of buying them), I accepted a 500+ cut order which still took multiple 24×36 sheets, but can you imagine how many small sheets that would be? Even when I don’t “need” the space, I have workable area to stage my next cuts. I really feel that the Mira 9 is the perfect size laser for my flat work!
Wait, what? Flat work? What are you talking about now? I have a second Mira – she’s a Mira 7! Now I have talked about how perfect the 9 is – so why a 7? Well, I use that machine primarily for tumblers. I keep my honeycomb tray out and my rotary installed. Keep checking back, more to come on that topic!

But is she fast?
We love engraving tumblers on our Mira 7 from Aeon Laser USA.
This beautiful peonies cup took about an hour to engrave but the beauty that it adds is priceless! Coming from a tumbler background with our resin line, I know how people appreciate personalized, custom drinkware . Growing into an engraving business was a natural progression for CestCreative and we couldn’t have picked a better company to partner with on that journey.
Our Aeon Laser Mira 7 as well as our Mira 9 is blazing fast compared to our original hobby laser, and tumblers wouldn’t even fit in that machine! We also have a variety of rotaries to choose from when we are engraving. From the basic but very capable Smart Rotary, our Multi-roller, to our Lens Digital PiBurn (we have v4.0 and the Grip!), we keep our lasers busy. Fortunately, our lasers keep us on time and prompt with our orders 😉
Variety is the Spice of Life
So I talk A LOT about the machine, but what about what I put into the machine? If you follow me on socials (@cestcreative on all – links at top of page) you’ll find projects that I don’t even have listed on this website. Hmmmm…let me try to list everything that I have lasered….
Acrylic – hands down my favorite material to work with! My product displays, custom clients (people for whom I cut their designs), earrings/jewelry, QR code displays, keychains, awards, bagtags, ornaments, ….so many possibilities, colors, textures, dimensions!
Wood – signs, earrings/jewelry, keychains, awards, ornaments, displays…wait that sounds a lot like the acrylic list! Almost everything I make in those categories can be made in either material or combined together in the same project. One of my favorite mixed media projects were awards that I designed, cut from wood and acrylic, and engraved. Add to this category all of the wood items that I have engraved such as coasters, cutting boards, picture frames, charms…
Slate – engraves beautifully
Leather and leatherette – so many items!
Glass, powder coated items, doormats, silicone,….
All of these items turned out beautifully thanks to my AEON Mira lasers!
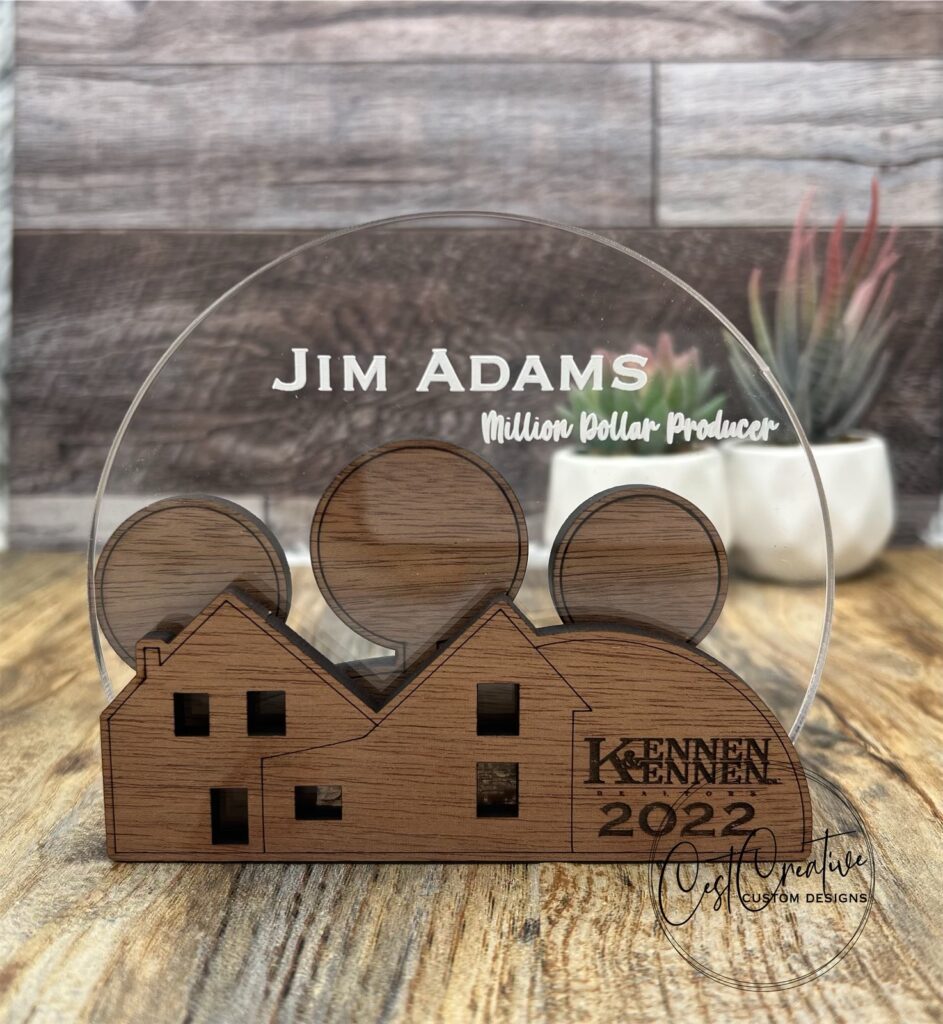
#AEONFAM
How do I put into words how much I love being a partner with Aeon Laser USA? I talk about the machines, but what about the company behind the magic?
Some of the many things:
The customer success team – really everyone at Aeon is a part of the customer success, right? From logistics to technical service and everything in between – Aeon has your back. The great deals and specials and HELLO FREE LASER GIVEAWAYS!!! But it’s not just about the freebies its way bigger than that! Its the heart and soul that each and every employee puts into their job (is it really work if you love it this much?)
My salesperson helped me decide on the perfect laser / accessory combination – while sending me videos taken in his own kitchen …. and while I was waiting on my laser baby, his wife was having a real one!
I have had several calls with the leadership team – all the way up to the most senior members . They engage with their partners and ensure that we are informed, educated, supported, and most importantly, that our Aeon Lasers are functioning perfectly.
Technical support (the official Customer Success Team) – sometimes we need a little help that goes beyond the quick question in the Facebook group, and that’s ok! Ive had the pleasure of working with many (maybe all?) of the team members and I’ve even danced the night away with several at the last Partner Event! But don’t be fooled when I say I have talked to them all – it doesn’t mean that my laser has problems, sometimes its a quick ask about how to do something easy, but they never make me feel like a bother/silly for asking. I actually have a whole story about the technical support, so get ready for that one! Its a doozy!
The community – since becoming a partner I have been so blessed to have met so many people – top influencers who share their wisdom and business tips , fellow owners who are passionate about their machines and products, and newcomers who are thirsty for knowledge. I have built lasting friendships that go beyond just sharing the latest laser tips; I have a whole laser family!
The Phoenix from the Flames
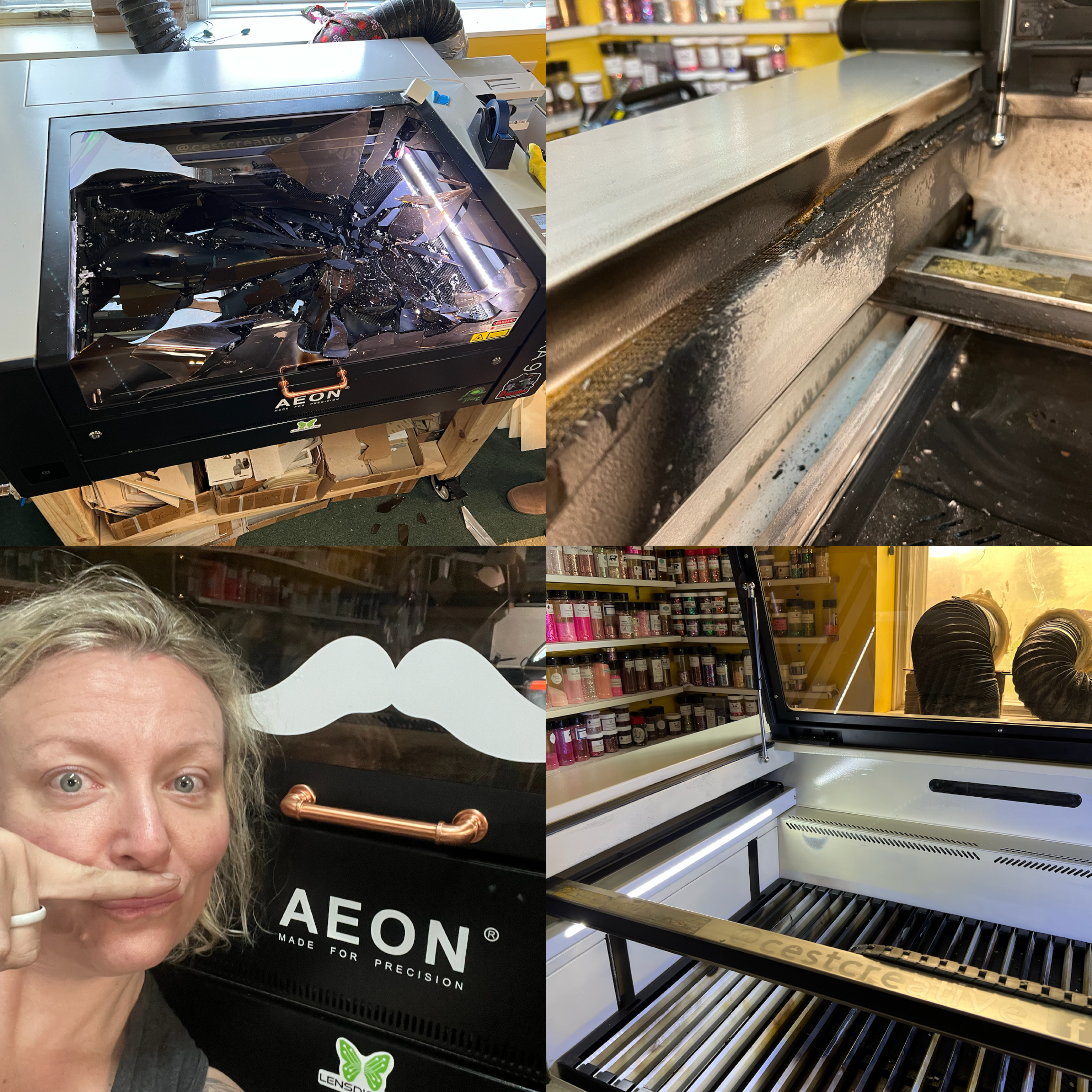
This is the actual post that I made in The Laser Outpost group – when it was raw and ongoing…
It’s taken me a week to write this, not out of shame, not out of embarrassment – but because I have spent the last 7 days working with the wonderful folks at Aeon Lasers USA and my dear friends in the community to re-emerge with a plan to get back up and running while triaging all of the things that went wrong. Who am I kidding. It wasn’t “all the things”. It was one thing. Me. 👉🏻🥸👈🏻 Now hear me out. This isn’t a pity party, this isn’t a blame game. This is Christine being Christine – being real. It’s a story that (I feel) needs to be shared.
I am a rule follower, I am safety conscious. How many of you have mowed your yard wearing steel toed boots? No? Just me? I work for a chemical company and used to be out in production. Talk about safety measures. I lead safety discussions during my staff meetings. You see where I am going with this?
I’ve seen posts of burned up machines and thought to myself – how could they let that happen?
Well, im here to tell you how it happened to me. Again, not looking for pity, and please save the shade – there isn’t anything you could say to me that I haven’t beat myself with already.
But here it is.
I broke the #1 cardinal rule. I walked away from my machine. I was 1h20 into a 1h 38 acrylic cut. It was the 5th of 7 sheets. It was really late at night. I had shut down for the day, went to dinner with my family, came home and said ooooh just. one. more. run. Tomorrow is Easter and I don’t want to be tethered to the laser. One more sheet.
At 1h 20 I could hear Trish and my mom upstairs, I needed something to drink, I hadn’t had any issues all day long…. How bad could it be?
Well when I went upstairs, Trish and mom didn’t know the laser was still running – I never emerge from the shop until I’m done. So when I sat down, slowly sinking into the couch, they didn’t think anything of it. Not even when I fell asleep.
Yep, there it is – not only did I walk away, go upstairs, I fell asleep. When I came to I had no idea what time it was – what I had been doing. And mom and Trish said, cmon let’s get you to bed.
Meanwhile in the workshop…… a fire had started in my machine. My 24×36 sheet of acrylic cuts burned for however long it took to completely consume the material, scorch the inside, melt the belt, and shatter the lid.
There are a few things that worked in my favor. The job finished and the head homed rear right. The fire was concentrated front left. So overall the damage “appears” to be contained to those parts and in the main cabinet. Electronics, mirrors, etc are in a working state. Of course we shall see once we try to get the big girl operational again. Also my external exhaust pulled most of the smoke out of the machine and out the window. The smell of fire was only faint and probably due to the lid giving up.
I might be bold enough to say my machine saved my house. It held the fire until there wasn’t anything left to burn.
The first person that I need to thank in all of this is Liz – it was Liz who snapped me out of it, and said ok here’s what you need to do….. Step 1 put in a ticket…….
And that’s where it started. Monday – Friday I have been working with the wonderful people at Aeon assessing the best path forward for repair, talking to my sales guy to see what the lead times are on a new machine, cleaning up debris, outsourcing the big jobs my little Glowforge can’t handle, negotiating with a seller of a used machine, and as I write this I am 8.1 miles from a Mira 7 that’s awaiting pickup in New York!
To say it’s been a week is an understatement. But I wouldn’t be here with such a focused, positive outlook if it weren’t for the wonderful people in this community. Too many to name in the post but you know who you are. #aeonfam
Well it’s about time for an update! As you saw I have a new belt but what else?
First things first – please do not take my experience as the standard. I am sharing the specifics as it relates to my machine and decisions that were made based on lengthy discussions and evaluations of my unique situation.
Fire is incredibly destructive – not just the flames, but the smoke and the heat generated – it can damage parts that you cannot even see. While I am optimistic that we have passed the greatest hurdles, there could be damages that I don’t yet know – including (but not limited to) laser tube damage.
But enough with the stern warnings and disclaimers – what’s going on with Large Marge….. I mean Burnt Reynolds!!!!?
For the first week – every day since the ticket was entered I was sending pictures and videos to Aeon. I started by picking out all of the glass, and acrylic remnants. I pried the melted pieces off of the crumb tray and attempted to wash it. I scrubbed down the inside, peeling off the melted lid seal, LED lights, and camera. She sure wasn’t pretty anymore. With the help of a shop vac and a tiny hose attachment I vacuumed out as much debris as I could.
Opening the side panels was scary. I was expecting to find damages hidden “behind the scenes” but did not. I traced every visible wire, tube, etc looking for any signs of melting. Even though my camera was gone – no, seriously there were no traces that I had a camera except the USB cable magically was still attached and running inside the lip of the lid. I traced it, carefully removing the clips and followed it all of the way to the source and unplugged it.
I was then able to remove the lid….the frame was still attached by one hinge and 2 gas struts. I easily removed them. I actually debated for a bit about temporarily putting acrylic in my lid. But (1) the space is larger than the largest piece of acrylic I had on hand and (2) the glass in the lid is tinted to help protect our peepers 👀. While I do have my glasses, I didn’t want to risk my family if they approached the machine.
I worked on the LEDs on the left. Well that is still a work in progress but I did get everything removed including the wire. I traced this back too but lucky enough there was a plastic wire connector near the top. I disconnected the melted piece there and verified that the remaining wire was unscathed.
Once she was all cleaned up, wires tied off, parts in labeled bags, I waited for the experts to tell me what was next…..well, not exactly. See I’m incredibly impatient, stubborn, and determined – so I couldn’t sit and wait. I decided to plug her in and see if she turned on. And she did. But what else? I was so nervous, I asked Trish what she thought and she said, “well, what’s the worst that can happen, you’ve already caught it on fire!” So I moved the gantry. Forward and backward. I could only move the head a little bit because the belt was damaged on the far left and I didn’t want it to go around the roller or snap, etc. but I was able to move it left about 4-6 inches. The red dot was there. But would she fire? I got a scrap and hit pulse. 😱 there it was! The tiny little burn mark that told me this machine was a tank and was far from dead.
… after all of her parts were replaced, she got a nice coat of Almond paint on the inside, the LED panels were shining bright, and we were once again ready to FIRE THE LASER!